Maximising efficiency – the ERP solution for engineering and manufacturing businesses
Specialised engineering and manufacturing businesses are always looking for ways to gain efficiencies, but the nature of their operations make this challenging. Because they produce customised, ‘job-based’ outputs, each individual job is handled in a specific way, with the design and production process full of potential challenges.
A business might focus on custom or specialised manufacturing, or engineer-to-order (ETO) products; they're all asking the same questions:
• What are the most important production/job costing management software capabilities that make efficiency gains possible?
• What do we look for in a technology-driven solution that will increase the efficiency of our operations?
When you're producing complex, high-value, ETO or innovative products, an ERP solution that can not only handle the complexities of what you do but also streamline your business processes is an essential tool. You need a solution that supports your manufacturing or engineering processes and all your other business activities in one integrated system. Using traditional, specialised, stand-alone systems is time-consuming and resource-hungry, and processes tend to become bogged down until no-one's getting the information they need.
At Endeavour, we work with custom manufacturing and precision engineering businesses to implement ERP solutions aimed at improving their efficiencies and streamlining their business processes, within the constraints of their complex and variable production process.
Our ERP offerings are the solutions of choice, because they target a number of areas specific to manufacturing and engineering. Our engineering and manufacturing customers gain efficiencies in these areas:
- Quote templates
These capture standard items, labour and costs for similar jobs to enable cloning of templates each time a new quote is required. This minimises data entry, which in turn reduces or even eliminates errors. The templates ensure accurate pricing for quotes, hence protecting margins.
Once a quote has been accepted, a job can be created with just the press of a button. Again, this ensures not only data accuracy, but that data entry is required only for any overrides.
- Inventory tracking
As products go through an engineering process, the transformation of that product from one form to another can be accurately tracked and costed to ensure correct identification and costs. For both engineering and manufacturing businesses, there are:
- Multiple units of measure – these are required to provide greater flexibility in both purchasing and selling functions, as well as the ability to buy or sell in different unit of measures (UOMs) to leverage on pricing and discounts.
- Multiple warehouses, locations – flexibility to identify bulk storage, quality control or quarantine locations.
- Job costing
A job that's been created from a quote will inherit all the details at the quote level. This eliminates errors generated by a manual job creation. Additionally, timesheets are usually captured ‘on the job'.
For jobs that are done remotely, real time data capture can be easily done via browser extensions and/or mobile app extensions, hence ensuring online updates of related costs to the specific job. These browser extensions and/or mobile app extensions can also be utilised to facilitate purchase order creation should additional parts and/or consumables be required for the particular job. Optional approvals routings can be set up for such purchases to streamline the flow of data and processes.
Job costing also ensures the correct allocation of jobs; the right person with the relevant qualifications is assigned to the job. Plus, the flexible invoicing and WIP costs tracking functionalities will ensure accurate revenue and costs capture and reporting at period end or when the project or job is completed.
- Service requests
These are scheduled online so that the appropriate resources are allocated to the relevant service or job, the relevant service person is notified by email, ensuring prompt response to the service request and timesheets can be entered ‘on the job’ to ensure prompt update and invoicing.
- Financials and Reporting
Financial information from the above operational modules integrates directly into the financial systems, resulting in reduced time required to process month-end activities, and ensuring financial reporting is timely and accurate. Not only that, but:
- Flexible report writers caters for different reporting requirements, such as financials and non-financials reporting, web-based queries and reports
- There's also an embedded Business Intelligence analytics and reporting feature for enhanced visualisations of KPIs, using dashboards
Harnessing Endeavour’s ERP solutions with a proven Job Costing application is essential for any engineering or manufacturing business looking to streamline and gain efficiencies in their daily operations.
The reduction of errors and manual data entry alone is a major time-saver; the automated approvals and quotes processes are streamlined and designed to keep projects moving through each phase smoothly. Relying on stand-alone systems or continuing to use outdated, legacy software solutions will not only slow down your business processes, but the errors they generate can be detrimental to your business reputation.
If you’d like to learn more about how Endeavour can help your custom manufacturing business maximise efficiency and stay ahead of the competition, read this guide to enabling business growth.
You May Also Like
These Related Stories
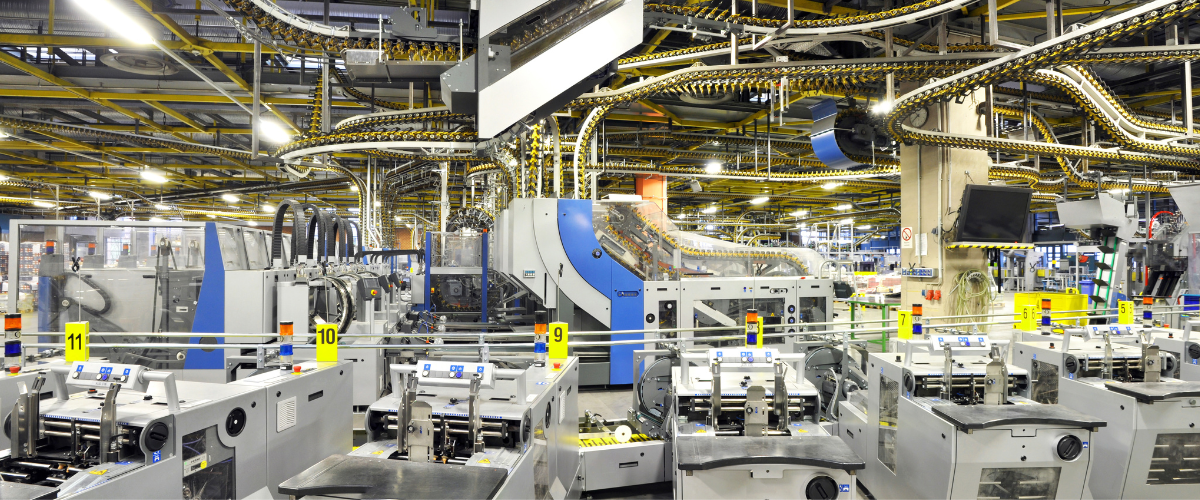
Excellence in the building products sector
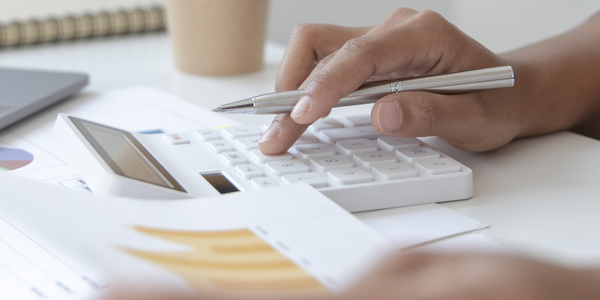
Facing the challenges of shifting market conditions and rising costs?
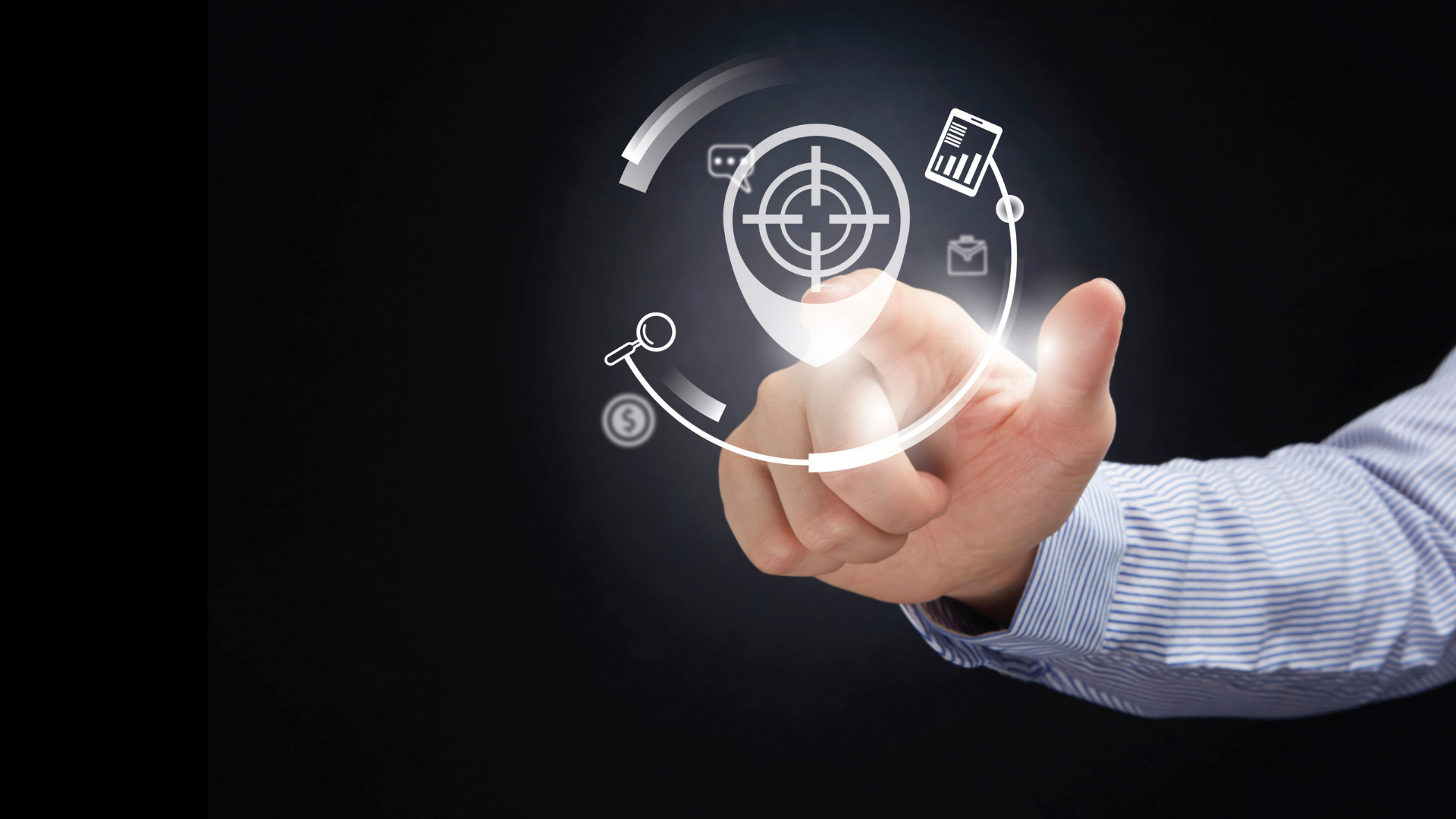